Friction stir welding cold plate
Profile + welding
Liquid-cooled heat sinks processed on the basis of profiles. These radiators are more in shape, have plate type, have channel type, and have a combined type. The general production principle is to process and weld on the basis of profiles. The profile and the joint pipe are combined into a unitary liquid-cooled heat sink.
The cold plate flow channel is directly formed by the extrusion process, and then the cycle is opened by the mechanical addition method, and the welding process is usually performed by friction welding, brazing welding, etc., the process has high production efficiency and low cost; and is not suitable for excessive heat dissipation density. The application is not suitable for applications where the surface has too many screw holes to limit the water course or reduce reliability. Mainly used in: power battery water cooling heat sink, water separator and standard power module integrated heat sink products.
Machining + welding
The water-cooled plate adopts the machine-added mode, and the internal flow channel size and path can be freely designed. It is suitable for thermal management products with large power density, irregular heat source layout and limited space. It is mainly used in: wind power converters, photovoltaic inverters. The design of heat dissipation products in the fields of IGBTs, IGBTs, motor controllers, lasers, energy storage power supplies, and supercomputers is less used in power battery systems.
The microchannel heat sink is also a heat sink manufactured by a combination of machining and welding processes. It is more complicated to manufacture than other heat sinks. Microchannel heat sinks are generally used on machines with large heat dissipation and concentrated heat dissipation. The way of the channel is because the water channel is wider and more uniform, and it can quickly take away the concentrated heat. However, the micro-channel liquid-cooled heat sink manufacturing process is also relatively complicated, generally using a machined microchannel, and then using a friction welding process for welding, and the manufacturing cost is also high.
Die casting + welding
The die-casting process is a very mature and widely used forming method. With the rapid development of new energy vehicles, it has become the first choice for mass production of motor controllers, power battery pack trays and heat-dissipating boxes, but it is necessary to control the die-casting impurities in the process. Problems such as stomata, conservative use of sealing ring method or friction welding, all need to improve the reliability of the process to avoid water leakage. Die-casting and re-welding, good process control, stable process, and batch delivery capability. In addition to the friction welding process, some water-cooled plates are also brazed or vacuum brazed.
Application areas:
Fiber laser cold plate
Military transmitter cold plate
Optical communication cold plate
Electric vehicle control system cold plate
IGBT cold plate
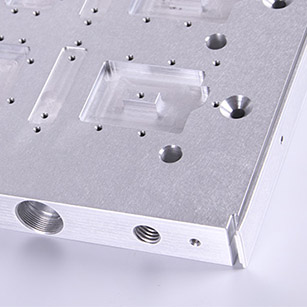
Request Catalogue
Request Tech Details
If you have any doubts about the product, please feel free to contact us by phone or email us. We will provide 7*24 hours service, sincere thanks.inquire@zhcooler.com
+86 15603820837